Project General Information


Project Type
Location
OFFICES
RETAIL
PRINT SHOP
LEVEL 1 RETAIL
EAST GARAGE
APARTMENTS/ AMENITIES/ WEST GARAGE
Owner : Hekemian & Company http://www.hekemian.com/
Architect : Design Collective Inc. http://www.designcollective.com/
General Contractor : Bozzuto Construction Company
MEP : Allen & Shariff http://www.allenshariff.com/
Civil /Site development Engineer : Gower Thompson
Structural Engineers : Morabito Consultants
http://www.morabitoconsultants.com/
Telecommunications: Data watch
Project delivery method : GMP – Guaranteed Maximum Price
Building Occupancy:
The existing Rotunda is owned by Hekemian and managed by Manekin management. Because of the presence of different retail spaces the occupancy varies depending on who the tenant may be.
The new construction has retail spaces as well as apartments. These spaces would be occupied by tenants renting the apartments and retail spaces but manage by the same company.
Total Square Footage: 857,598 GSF
Number of stories above grade/ levels: 5 - 8
Dates of construction : September 2013 – December 2015
Actual Cost of Construction : $100,000,000
BuiLding Codes: International Building code, BOCA, Baltimore City Code, NFPA
Zoning code: not available at this time
Historical Background
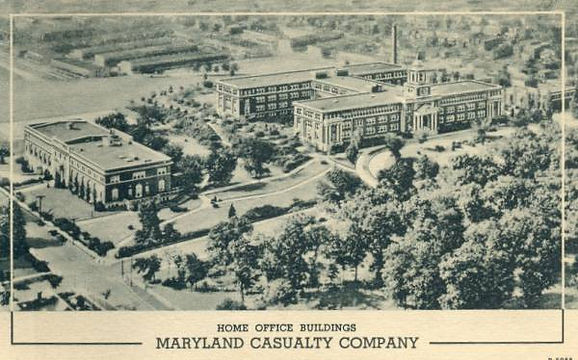
The Maryland Casualty Company purchased the
Dulin Estate in 1919 and established on the twenty-five acres anextensive business campus that included a number of impressive amenities,
including a clubhouse with a dining room, an
auditorium that could seat 1,500 guests, a landscaped park, tennis courts, and a baseball diamond. The idea was to provide workers with an idyllic business campus removed from the hustle and bustle of the downtown area. What is now known as the Rotunda was the company's administration building. The H-shaped building features a distinct bell tower and 1921 Connecticut clock that exists today as a landmark of the Hampden community.
The Rotunda tower was renovated with a technique called “speckling” where workers thumbtack-sized dots of black paint on the tower's terra cotta.
Building Enclosures


Roofing
As shown in the picture above the new construction has four major Roof types. Roofing for the last level of the cast-in place west side garage, roofing for the building E & F, roofing/ceiling/flooring for the east-side courtyard and the unaccesible roofing for the buildings A, B, C & D.
The TPO Roofing system was used to construct all top of deck roofing on the new construction of the Rotunda. The most common differences amongst the roof type is the insulation and finish. The roofing above the unnaccesbile resident units on the 8th level have an R-38 unfaced batt insulation, while that of builidings E & F have a roof insulation of R-25 5" rigid insulation.
TPO roofing system sample section
Courtyard Yard Roof Detail
Facade/Exterior wall materials
The Rotunda’s façade is a combination of stone, brick, and terracotta. . Overall building envelope represents with masonry cladded wall and storefront window system.
The entire first level of the south façade has galvanized store front doors with glass windows covering at least 60% of the entire wall. The weather barrier used is the Typar which is similar and most common compettior to the commonly used Tyvek weather barrier.
Throughout the entire upper level apartments, different Vinyl window types (shapes and sizes) were used to accomodate for aesthetics, ventilation and daylighting into the apartmetns.

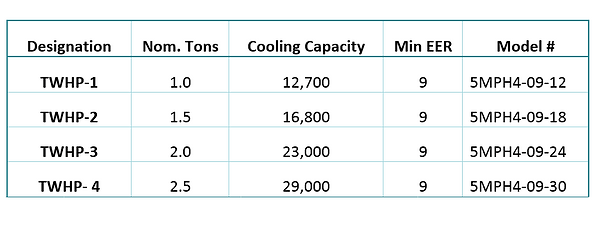
Mechanical System
APARTMENTS
All the units where mechanically designed to have operabale windows to allow positive presurrization of the spaces. The mechanical system used is the magic-pak electric heat pumps. Four different thru-the-wall packaged systems were selected to accomodate for th edifferent sizes of the various apartments. This is an qir-to-air heat pump system.
The packaged system has an EER up to 10.0 cooling efficiency and is completely self contained. There are no outside condensing units, external refrigerant lines or seperate cooling coils. Each system is indiviually metered and controleld for each apartment unit, with louver options for outdoor air intake. The packaged systems have a refrigerant system using high efficiency compressors, with copper tubing with enhanced fin coils. The refrigerant used here is the R410A refrigerant.
The system comes with fully insulated cabinet design that allows it to have a quiet operation within each apartment.
Summary of Mechanical Systems in the Building
Magic Pak Thru-wall Packaged Terminal Heat Pump
AAON CC-series outdoor system
Structural System
CLUBHOUSE
The Clubhouse is categorized into four different zones using four Split Heat pump indoor units with each outdoor unit on the roo top. The units nominal tons range from 5 tons to 14 tons, depending on what zone it is designated to serve. It features a split system modulating control to provide energy efficienct dehumidification, even with low sensible heat loads. Compressors and unit controls are contained within a single compartment isolated from the air stream for ease of service and queit operation.
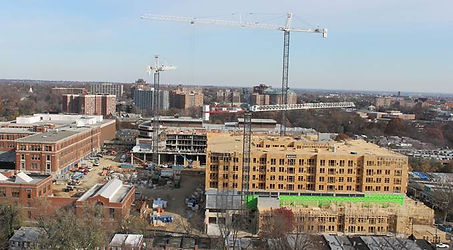
EAST SIDE - WOOD FRAMING
The Clubhouse is categorized into four different zones using four Split Heat pump indoor units with each outdoor unit on the roo top. The units nominal tons range from 5 tons to 14 tons, depending on what zone it is designated to serve. It features a split system modulating control to provide energy efficienct dehumidification, even with low sensible heat loads. Compressors and unit controls are contained within a single compartment isolated from the air stream for ease of service and queit operation.

WEST SIDE - METAL FRAMING
The Clubhouse is categorized into four different zones using four Split Heat pump indoor units with each outdoor unit on the roo top. The units nominal tons range from 5 tons to 14 tons, depending on what zone it is designated to serve. It features a split system modulating control to provide energy efficienct dehumidification, even with low sensible heat loads. Compressors and unit controls are contained within a single compartment isolated from the air stream for ease of service and queit operation.
Construction
EAST SIDE - WOOD FRAMING
The Clubhouse is categorized into four different zones using four Split Heat pump indoor units with each outdoor unit on the roo top. The units nominal tons range from 5 tons to 14 tons, depending on what zone it is designated to serve. It features a split system modulating control to provide energy efficienct dehumidification, even with low sensible heat loads. Compressors and unit controls are contained within a single compartment isolated from the air stream for ease of service and queit operation.
Lighting/Electrical
EAST SIDE - WOOD FRAMING
The Clubhouse is categorized into four different zones using four Split Heat pump indoor units with each outdoor unit on the roo top. The units nominal tons range from 5 tons to 14 tons, depending on what zone it is designated to serve. It features a split system modulating control to provide energy efficienct dehumidification, even with low sensible heat loads. Compressors and unit controls are contained within a single compartment isolated from the air stream for ease of service and queit operation.